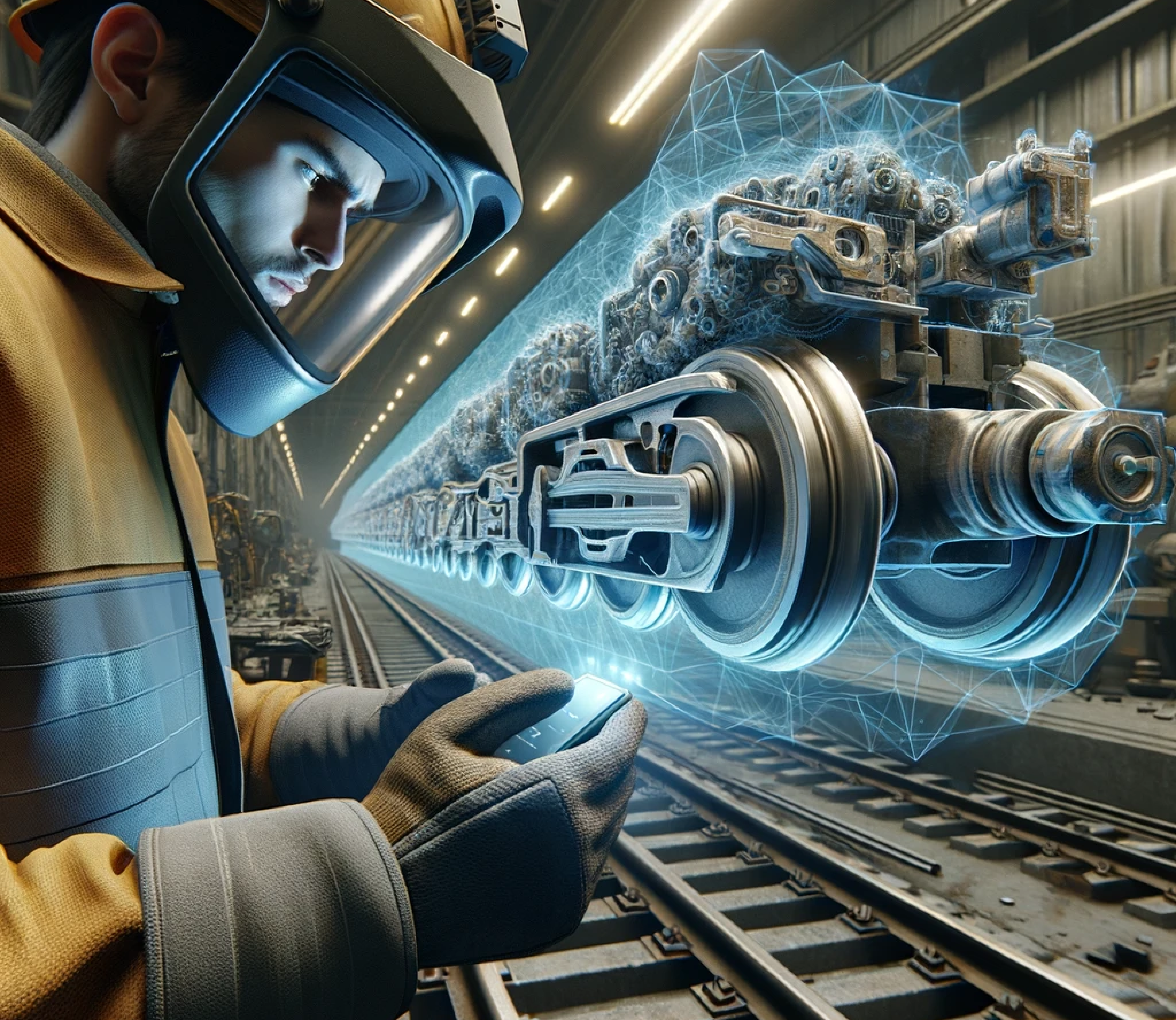
In the modern era where technology permeates every industrial sector, Virtual Reality (VR) has emerged with new and exciting applications. One such application is in the preparation of components for welding—a process in which VR plays a pivotal role, especially in harnessing the concept of Industry 4.0.
Dig in Vision provides advanced VR equipment and software that allows welding engineers and welders to test and optimize their welding processes before beginning actual work on the components.
Immersive Tech and Digital Twins in Welding
Through VR technology, users can import any 3D models of components that need to be welded. This capability allows for the precise examination of joint geometries. A crucial benefit is the ability to modify various welding parameters, such as voltage and current intensity, invaluable for setting up optimal equipment configurations. VR also enables engineers to verify and test constrained welding positions, critical in complex joint scenarios. The virtual work environment creates a digital twin of the component to be welded, ensuring every action can be meticulously planned and tested. This exemplifies the implementation of Industry 4.0 principles, where the digitization of manufacturing processes leads to significant efficiency improvements, cost reductions, and minimized risk of errors.
VR Training and Immersive Learning: Advancing Skills and Safety
With the ability to visualize components in VR, welders can better prepare for actual tasks. Testing different welding positions in a safe, virtual environment helps identify the most effective methods and positions, which directly affects the quality of the final welds. This not only enhances work efficiency but also saves time and financial resources that might otherwise be spent correcting unsuccessful welds. Furthermore, VR enables comprehensive training for welders, providing them the opportunity to practice and refine welding techniques without the need for real materials. This approach is not only cost-effective but also environmentally friendly as it reduces the consumption of raw materials.
Business Adoption and Industry Impact
This cutting-edge VR technology is already being extensively implemented in the welding industry within Western European companies, where it serves as a revolutionary solution for training processes. Welders can engage in intensive training sessions on component welding before entering the production floor. This strategic approach ensures that the initial part of the project is welded correctly, thereby eliminating the production of costly and time-consuming waste. From the first weld, welders are well-informed about how to proceed in terms of sequence and positioning, significantly enhancing the quality and efficiency of their work. The application of VR in welder training not only raises production standards but also ensures greater precision and predictability of outcomes. This is crucial in industries that demand the highest quality of welds, such as automotive and construction.
Future Perspectives: Transforming Welding with New Technologies
Introducing virtual reality into training processes has revolutionized the way employees are prepared, equipping them with the necessary tools to perform tasks effectively and safely at the highest level. The implementation of VR in the process of preparing welding components marks a significant milestone towards realizing the ideals of Industry 4.0. It enables engineers and technicians not just to optimize manufacturing processes but also to significantly enhance the quality and precision of their work. This instance demonstrates how modern technologies can transform traditional methods, opening new possibilities and perspectives for the industry.
Follow us on Dig in Vision’s social media platforms to learn more about our VR kits and their applications in the industry. Discover how modern technologies can support your work and professional development!
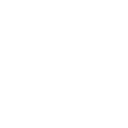
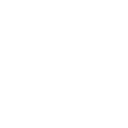
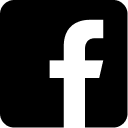
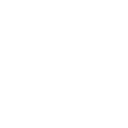
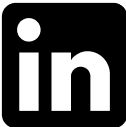
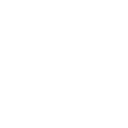
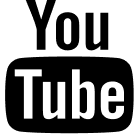