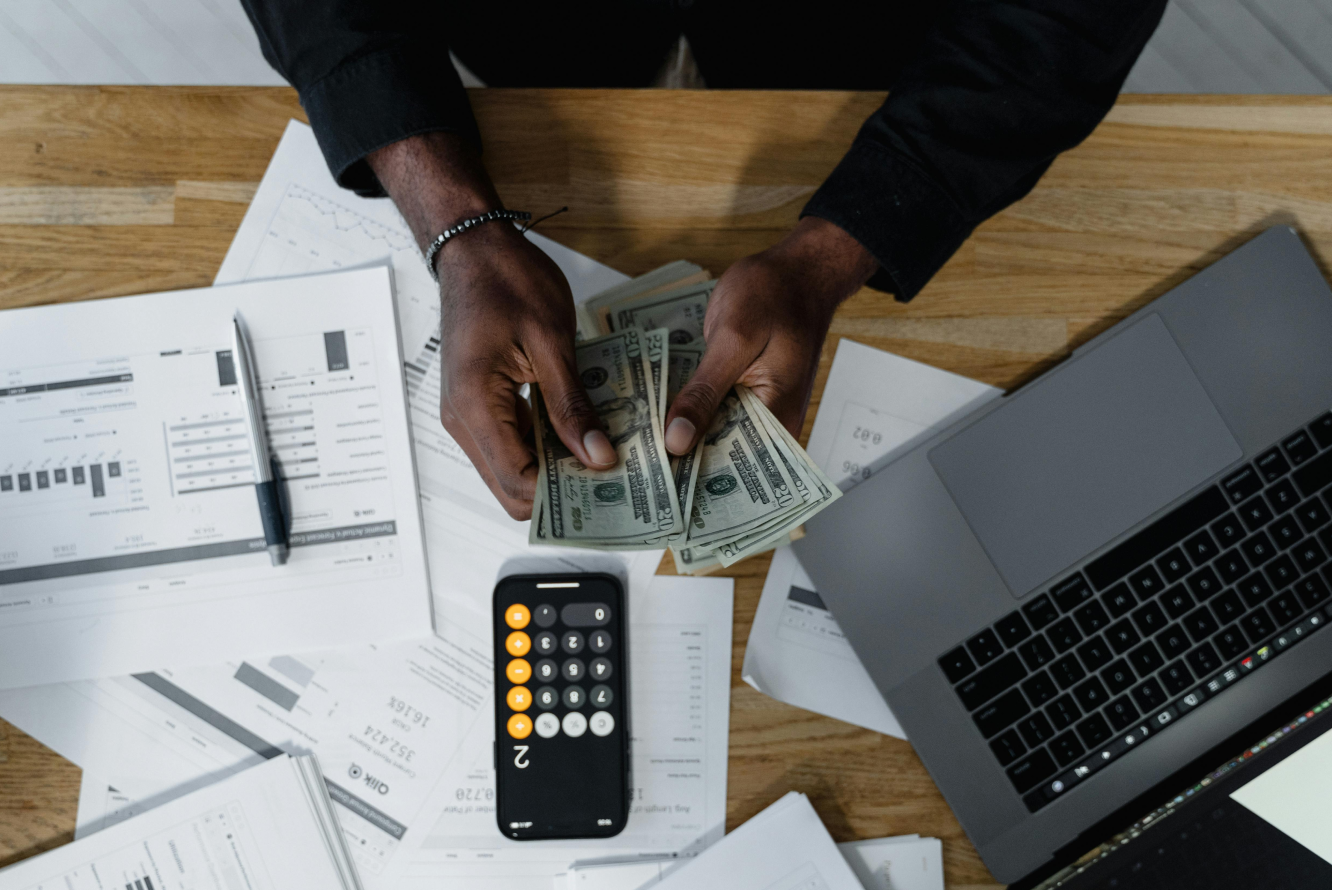
Welding training is essential for ensuring the qualifications required across various industrial sectors. However, the traditional teaching methods in this field are often prohibitively expensive for both students and training academies. In Europe, for instance, the cost of such a course can range between 2,000 to 5,000 euros, depending on the level of advancement and the duration of the training. These high prices are primarily driven by the need for substantial material consumption, including steel, gas, wire, electricity, and personal protective equipment, as well as the costs associated with maintaining workshops, servicing machines, and employing experienced welding specialists. It's estimated that consumable materials and machine maintenance can make up 40-50% of the total training costs, with up to 1,500 euros of a 3,000-euro course being allocated solely for these expenses. This significant financial burden is prompting training institutions to seek more cost-effective solutions.
VR Technology: A Game Changer in Welding Education
In response to the need for reducing training costs, Virtual Reality (VR) technologies are emerging as a revolutionary tool in welding education. Drawing parallels with pilot training, where up to 80% of learning occurs on simulators, VR is now being integrated into welding training programs, potentially covering 30-40% of the curriculum. This approach allows for substantial cost savings while providing a highly immersive and interactive learning experience. Dig in Vision, a leader in this innovative space, has implemented dual training for welders that combines traditional methods with cutting-edge VR technologies. Their projects across Europe, Asia, and Africa showcase the effectiveness of this dual approach in vocational education, particularly in industries demanding precise manual skills.
Enhanced Efficiency and Learning Outcomes with VR
The incorporation of VR into welding training offers unparalleled benefits in terms of efficiency and learning outcomes. In a conventional 8-hour training day within a real welding workshop, students might perform up to 20 samples due to the extensive time required to prepare materials and the limited availability of machines. In stark contrast, a VR environment enables trainees to complete 150 to 200 trials in the same time frame, significantly boosting the intensity and effectiveness of their practice. The use of a 10 VR samples to 1 real sample ratio allows students to refine their skills and develop muscle memory with minimal material costs, making this an exceptionally efficient training method.
Cost Savings and Future Potential of VR Training
One of the most compelling advantages of VR training in welding is the reduction in physical material needs, which directly translates into lower overall costs. While traditional training necessitates the purchase of steel, gas, wire, and the consumption of electricity and grinding tools—expenses that can comprise up to 50% of a course's total cost—VR eliminates these ongoing costs after the initial investment in software and equipment. Additionally, each VR participant can benefit from an individual virtual instructor, eliminating the need to share an instructor's attention among several students, as is common in traditional settings. Although VR training will never completely replace hands-on welding education, it serves as an ideal supplement that reduces costs and enhances learning. This fusion of modern technology with traditional methods has the potential to revolutionize vocational training, offering significant savings and preparing future specialists more effectively.
Stay Connected and Infor
Want to dive deeper into the world of VR welding training? Follow Dig in Vision on our social media platforms to stay up-to-date with the latest advancements and learn more about the Dig in Vision kit. Join our community today and be part of the future of welding education!med
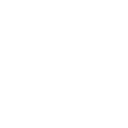
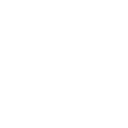
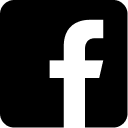
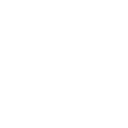
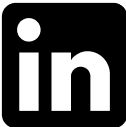
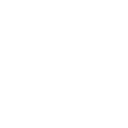
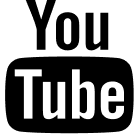